Boeing finds 787 pieces aren't quite a perfect fit
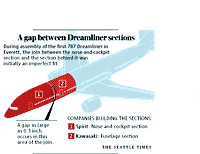
In theory, the giant plastic sections of Boeing's 787 Dreamliner that come in from across the globe all fit perfectly for a quick snap-together assembly in Everett.
But in the real world, it turns out there can be gaps.
Photos of the final-assembly process provided anonymously to The Seattle Times show the jet's first two forward sections did not fit properly when initially joined. On one side, there was a gap wide enough to stick a finger in.
The photos -- taken during the ongoing assembly of the first airplane, which is due to roll out in a month -- show a gap of 0.3 inch where the nose-and-cockpit section made by Spirit AeroSystems bulged out farther on the left side than the fuselage section behind it, made by Kawasaki of Japan.
Boeing said that within the past week the problem has been safely fixed and the gap eliminated. Company spokeswomen said the gap was a typical issue in putting an airplane together.
"The join in those pictures is now resolved," said 787 program spokeswoman Yvonne Leach. "It's not a problem now."
Her colleague, Mary Hanson, added, "It wasn't a perfect go-together the first time. There were a few challenges. We overcame them."
"In general, [Boeing's engineers] are pleased with how all the joints are going," she said.
Spirit spokeswoman Sam Marnick called the gap "a slight fit issue with the first barrel -- nothing unusual with a new program."
"Quickly resolved"
She said the matter "was quickly resolved and we learned as we moved onto the next one."
On the metal airplanes that Boeing builds, it's common in the assembly process for machinists to encounter gaps where parts are supposed to join.
"If it was metal, and it was only three-tenths of an inch, we'd have a party," said one former assembly mechanic who still works for Boeing and asked not to be named because he's not allowed to speak to the media.
But the Dreamliner was digitally designed on computers by engineers in Italy, Japan, Wichita, Kan., and Charleston, S.C., who collaborate by working on a single digital model of the airplane stored on servers in Bellevue.
Boeing adopted the digital design and collaboration software to ensure that on the 787 the massive composite plastic sections would fit together when they arrived for assembly from far-flung locations.
Still, Hans Weber, an industry technical consultant and president of San Diego-based TECOP International, examined the entire sequence of photos and sees no cause for alarm.
"It doesn't strike me as all that unexpected," Weber said. "In the process of putting those splice plates on one side, they distorted the structure a bit. That's not unusual. The structure distorts fairly readily."
Fixing that is typically done, he said, by disconnecting interior fittings -- such as floor struts and other supports -- that put pressure on the fuselage's outer shell. Then workers pull the section into alignment and reattach the fittings.
But Weber warned that such problems could be more likely and more difficult to deal with when the 787 fuselage sections start arriving fully stuffed with all interior fittings.
Boeing has said the initial airplane sections are arriving from the major partners not fully completed. But when production is up to speed, those sections will come pre-installed with everything from wiring to hydraulics and insulation.
Such "stuffed" fuselage sections could be more distorted by all the pre-loaded interior fittings and systems, Weber said.
The photos appear to be 787 program photos taken in the course of the analysis of the problem and shared with Boeing's partners Spirit and Kawasaki.
The photos of the fuselage gap came with descriptive text and labels, apparently showing engineers at Boeing and a "Spirit onsite team," brainstorming ways to address the problem.
"There are multiple plans being discussed to address this condition," the text says. "Some folks believe they should bust loose the [Spirit fuselage section passenger cabin] floor at the aft ... and 'pull it in.' Others think the solution is to bust loose the splices on the frames in the last 2 bays."
A later entry updates the issue and suggests "disconnecting some of the stanchions on the LH side and pushing/pulling on the [Spirit section] in an attempt to align it to the [Kawasaki section]."
That sounds much like the pushing and pulling and heaving that occasionally goes on in metal-airplane assembly.
According to Boeing, some of the above techniques finally worked, and the 787 is one step nearer to its celebratory rollout July 8.
Dominic Gates: 206-464-2963 or dgates@seattletimes.com
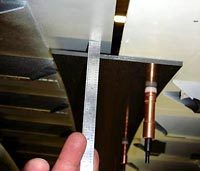