Newest Boeing jet rises from spools of thread
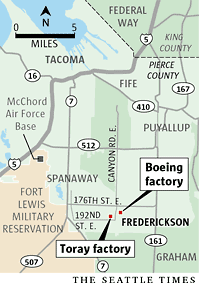
FREDERICKSON, Pierce County —Inside the "creel room" at Toray Composites America, hundreds of spindles squeak as they turn, steadily unwinding bobbins of black fiber.
The long, flat threads of carbon converge and feed into a machine that squeezes epoxy resin deep into the fibers.
This is how the fuselage, wings and tail of Boeing's new 787 Dreamliner begin.
"Our raw materials are string and glue," said Earl Benton, Toray's director of sales and marketing.
Just across the road, the alchemy is completed. Boeing turns these threads into the tailfin of the 787, the world's first largely plastic airliner.
The 787 is a bet-the-company wager for Boeing, one that now hangs upon building it right, getting it to fly this summer and delivering its promised efficiency.
The Dreamliner's potential already has propelled Boeing back into the top spot in commercial aerospace. Airlines have ordered or committed to buy 475 planes. Competitor Airbus lags by a full five years in developing its rival A350.
To maintain that lead, Boeing is relying on a complex new global manufacturing plan. Except for the Frederickson-built tailfin, all major chunks of the plane will be built by outside partners and then flown to Everett to be snapped together.
At the same time, as if to impress the world with the ambition, prowess and nerve of its engineers, Boeing is making an innovative shift from metal to plastic that will change forever the way airplanes are built.
Now it's time to start putting the pieces together.
Wednesday, the tailfin is scheduled to be rolled out and trucked north to the jet's final assembly site in Everett.
That's where Boeing plans to unveil the first completed 787 Dreamliner in July. The selected date: 7-8-07.
A vision in plastic
When you look at a Dreamliner sitting on a runway, almost everything you'll see will be carbon composite plastic.
"Say plastic, and people think of Mattel," said Phil Lathrop, a composite-plastics expert at Boeing Frederickson. But this is not the mass-production material that is melted and then molded into plastic toys, cafeteria chairs or computer casings. "We're not just stamping out fuselage sections," he said.
Instead, the airframe structural pieces must be built up, using layer after layer of carbon-fiber tape — Toray's end product — and then cured to hardness in a high-pressure oven.
The result is a structure that's light and strong, won't corrode and isn't subject to metal fatigue. And the plastic pieces can be built in huge sections, requiring far less final assembly work in Everett.
The edges of some structures on the 787, including the tailfin, are metal. And metal is used under the skin at some points to give structural strength. That metal makes up half the weight of the airplane.
But almost the entire outer skin of the 787, and much that lies beneath it, is made from the Toray raw material.
"This is what I consider an all-plastic airplane," Lathrop said.
Fuzz balls and glop
Boeing's global partners, from Italy to Japan, all rely on Toray's Frederickson plant to produce their carbon-fiber tape.
Entering the plant, a visitor dons a lab coat, hard hat and safety glasses, slips hospital-style blue plastic booties over shoes and walks through an "air shower" to blow off dust particles.
"We're very concerned about contamination," said production superintendent John Ward, leading the way to the creel room.
A creel, like something out of a 19th century textile mill, is an array of parallel bars holding bobbins of tightly wound fiber. Each of the six creels at Toray has as many as 500 bobbins, and each bobbin holds up to 19,000 feet of fiber.
As the fibers unspool, they line up to form a wide sheet of parallel threads that feeds into a resin-infusing machine.
Sometimes the filaments separate, creating a small imperfection that must be removed. Before the sheet of fibers enters the machine, a worker reaches over and plucks off something to intercept such a defect.
"He's removing a fuzz ball," Benton said.
Meanwhile, in a much messier room, another ingredient is readied.
Amid empty containers coated with gloppy drips, epoxy resin and chemical hardeners are mixed in what resembles a giant cake mixer.
The beige-colored result, with the consistency of batter, is poured into metal molds the size of kitchen baking pans and frozen to suspend the hardening process.
Later, the solid slab is melted and dripped into a machine that applies a thin and precisely calibrated film of resin onto sheets of paper.
The carbon fiber is then squeezed between two sheets of this coated paper inside a resin infusion machine. Heat and pressure impregnate the carbon fiber with resin and hardener. Out the other end comes a wide black sheet, 3-foot or 5-foot wide depending on the machine, with backing paper retained on one side.
For Boeing, this tape must be cut into 6-inch or foot-wide rolls. As it comes off the cutting machine, two women inspect it for imperfections, watching for those fuzz balls. They remove any defects with scissors, then splice the tape back together.
Vacuum-packed and frozen, the broad rolls of tape are ready. Some go across the street to Boeing. Others go across the world to Boeing's 787 partners.
The plant supplies Mitsubishi, Fuji and Kawasaki in Japan, which respectively make the 787's wings, its center fuselage structural box and a fuselage section; Alenia in Italy, which makes the horizontal tail and midfuselage sections; Vought in Charleston, S.C., which makes the aft fuselage sections; and Spirit AeroSystems in Wichita, Kan., which makes the forward fuselage and nose of the airplane.
This fall, Toray's Japanese parent company will open another composites plant in Japan to supply the 787 partners there. But the Frederickson plant, running four shifts 24 hours a day, will continue to supply the 787 partners elsewhere.
Toray, which has supplied the tape to build 777 composite tails at Boeing Frederickson since 1993, last year doubled the factory's capacity. An expansion of similar scale is in progress to further prepare for the 787 work .
Toray is hiring, too. The work force, now at 325, could rise as high as 400 by mid-2008 when 787 production gears up. Total investment in the Frederickson plant has reached about $100 million, Benton said.
Robots at work
Across Canyon Road from Toray, about 600 people work inside Boeing's Composites Manufacturing Center. Because of the lean design of the 787 manufacturing process and a ramp-up in staffing last year, Boeing projects only modest increases in jobs as it adds production of 787 vertical fins to the current work of producing 777 tails.
Machines build pieces of the 787's 33-foot-long tail by layering sheets of the tape one upon the other.
The rolls of carbon tape are first loaded onto computer-controlled robotic tape-laying machines made by Cincinnati Milacron.
Beneath one such large machine, two long flat platforms lie side by side. On one, 777 tail skins will be built up; on the other, 787 tail skins.
Zipping back and forth, the machine lays a short strip of tape, cuts it, then lifts, swivels and lays another strip at an angle to the first. The cuts are precise enough to slice the tape but leave its backing paper untouched.
The robot methodically builds up the tail skin layer by layer.
How many layers? At the tip, where the loads are lighter, the skin may be as thin as 20 layers of tape, said senior engineering manager Randy Taylor. Next to the fuselage, it's more than 100 layers thick.
Every so often, a worker must tidy up behind the machine, reaching across the skin and cleanly tearing off excess pieces of tape left behind as the robot executes a particularly intricate cut.
The machine will build skins but also ribs and spars — the inner skeleton for the tailfin structure.
After build-up, these tail pieces are vacuum-packed in plastic sheeting and put into one of three massive high-pressure ovens, called autoclaves. The two larger autoclaves are 30 feet in diameter and 60 feet long.
Curing the pieces at 350 degrees for about eight hours hardens the resin and produces a superstrong, light plastic structure. The rough edges are trimmed to specification with waterjets made by Flow International of Kent.
Flexible assembly
Making the pieces for the tail from the Toray tape is similar for either jet.
"It could be a 777 one day, a 787 an hour later," Lathrop said.
But assembling the tailfin is dramatically different for the Dreamliner than for its 777 neighbor. Even though both tails are made from composite plastic, the way Boeing puts together the 787 tail demonstrates its new flexible concept for airplane assembly.
The 777 tail is put together like this: A massive fixed framework suspends the fin vertically while dozens of workers on surrounding decks drill and fasten pieces in place. Massive overhead cranes move the sections from one big fixture to the next.
The 787 tailfin, by contrast, comes together on wheeled, moveable equipment that holds the structure level in a horizontal position. Workers adjust the height to get under it or work the edges.
Using a small hoist that moves between the stations, one person can flip the tailfin while others steady it with guy ropes.
The process needs few mechanics. The lateral ribs of the tailfin structure are designed to snap into place between the longitudinal spars.
A robotic driller — a FlexTrack machine, made by Everett-based Electroimpact — crawls along the tail skin to automatically drill and countersink fastener holes.
"We drill 3,000 holes in the skin," said lead assembly mechanic Michael Halbert. "Ninety-eight percent will be drilled with the FlexTrack."
Unlike its 777 cousin, the 787 tail is rolled from one station to another without a big crane. Everything is flexible.
On the 777, mechanics consult paper drawings for technical details. On the 787, no one futzes with paper. Large flat-panel screens to the side display all the specifications.
The process is so streamlined, Taylor said, the plant could assemble one 787 tailfin a day. That's about twice the pace needed even if Boeing ramps up to 10 airplanes a month as expected.
"The first parts are fitting together like a glove," he said. "We're ready to go to full rate right now."
In late February, the very first 787 production tailfin sat in the Frederickson plant's next-to-last station. The only piece missing was the leading edge assembly, made in Shenyang, China, with an aluminum edge and a fiberglass and paper-honeycomb skin.
That piece is to be attached today, completing the tailfin for Wednesday's rollout.
Delivery of this fin to Everett will mark the beginning of the airplane's final assembly process. The first Dreamliner is scheduled to fly in late August and enter service next year.
To accomplish that, Boeing must assemble the first 787s, then prove to aviation regulators in flight tests that this new plastic jet is as reliable, robust and safe as one built in the traditional way.
"This is something that's kind of new to the world," Taylor said. "It's a big leap from a metal airplane."
Dominic Gates: 206-464-2963 or dgates@seattletimes.com
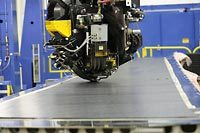
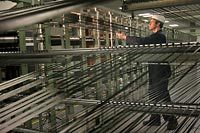
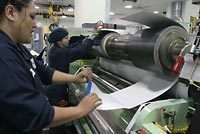
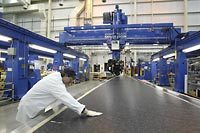
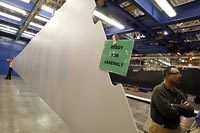
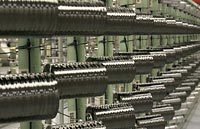
The raw materials
The plastic airframe of the 787 starts out as "string and glue," as an executive of supplier Toray Composites America puts it.
The string: Carbon fiber is derived from an oil-based polymer. Toray produces the fiber at its plant in Decatur, Ala., where the polymer filaments are spun into thicker flat threads, then treated at high temperature to increase tensile strength and stiffness.
The glue: The glue is made from epoxy resin mixed with chemical hardeners. The epoxy molecules are long polymer strands, like spaghetti, with linkage areas along the strands. The hardener allows those linkages to lock together when heated, turning a viscous liquid to a plastic solid.
Source: Toray
Why build a plastic jet?
Carbon-fiber reinforced plastic has advantages over aluminum:
Strong: Carbon fiber laid in precise configurations provides optimal strength where loads are heaviest.
Light: The plastic construction is up to 30 percent lighter than aluminum. Less weight means the plane burns less fuel.
Doesn't corrode or fatigue: Metal fatigues because of repeated stress over time, and it corrodes with exposure to moisture. Plastic does neither.
Reduces maintenance: Without corrosion and metal fatigue, a 787 will require a full heavy-maintenance check every 12 years, Boeing estimates, compared with every six years for a metal jet such as the 767.
Allows fabrication of huge pieces: A one-piece fuselage section replaces 1,500 sheets of aluminum and eliminates as many as 50,000 fasteners.
Nicer air, a better view for passengers: Boeing says it can keep the air that passengers breathe moister and more pressurized because the one-piece plastic fuselage sections are stronger, sealed more tightly and won't be damaged by humidity. The strength of the structure also allows bigger windows.
Source: Boeing