Boeing's Auburn plant takes new flight path
Management is shifting Auburn away from making basic parts for existing jets.
Instead, the site will focus more on higher-level specialty work and, in particular, on helping develop and test technologies for new airplane programs such as the 7E7 or new derivatives of current aircraft.
Yet for many employees and union leaders, one idea central to the strategy is deeply unsettling: Boeing aims to develop cutting-edge processes to where they can be outsourced to suppliers — then to move on briskly to the next new thing.
So while Auburn will do development work on the 7E7, it will get little of the production work.
"Being the best in the world at making components is not the focus of Boeing Commercial Airplanes," said Mary Armstrong, head of Boeing's fabrication division.
After helping develop new programs, Auburn will be "using our expertise to simplify the process to where we can move them to an outside supplier," Armstrong said.
"Then we get to use our expertise to take on the next product-development opportunity."
Armstrong's division employs 11,000 people worldwide, about 3,200 of them at the large Auburn headquarters. It is the largest supplier of parts to Boeing Commercial Airplanes.
With Boeing on the upswing, Armstrong rattled off a list of new programs Auburn is working on, or soon will:
• 7E7: Producing tooling used to build prototype parts of the fuselage and the wing box, as well as testing of those parts.
• Large cargo freighters: Supplying parts for the three specially converted 747s that will transport large 7E7 assemblies to Everett from Japan, Italy and the southeastern U.S. The modifications of those jets will be done elsewhere by a partner not yet identified.
• 747 special freighters: Producing parts kits for modifying 747 passenger jets into dedicated freighter aircraft. The modifications will be done in Asia.
• Multi-mission maritime aircraft: Producing parts for the Navy's converted 737 anti-submarine airplane, to be built in Renton.
The most exotic current work is the 7E7 prototype tooling.
No one has ever made a large commercial airliner almost entirely from composites — plasticized carbon fiber baked under pressure. Boeing is creating the manufacturing process in Seattle; the major 7E7 supplier partners will implement it in plants worldwide.
Inside the low, bland box buildings at the Auburn site, highly complex tooling and parts are taking shape.
A large curved panel of composite material — a test piece for the 7E7's fuselage — lies on a 5-axis milling machine ready for trimming.
In an adjacent bay, employees work on large pieces of a rotisserie tool — a huge spindle; a curved mandrel made from heavy specialized steel; an intricate steel construction with an egg-carton-like surface — that will be used to spin complete 7E7 fuselage barrel sections out of rolls of carbon-fiber tape.
Much of this tooling is headed for the Developmental Center on Marginal Way, where Boeing is perfecting the manufacture of big composite 7E7 fuselage sections.
But because of the new 7E7 business model and the new way this jet will be put together, Auburn's 7E7 involvement will be almost entirely in the development phase.
For instance, electrical and hydraulic systems are installed today on a typical Boeing airplane on the final-assembly line after the airframe takes shape.
On the 7E7, airframe sections will arrive from overseas partners with the systems pre-installed or "stuffed."
"We're not expecting a large amount of ongoing production work on the 7E7," Armstrong said.
That sounds like bad news for the large Tube and Duct facility at Auburn. Yet Armstrong insists Tube and Duct, which makes highly complex, hard metal parts such as a titanium de-icer for the 777, will thrive doing only high-end work.
To compete with European plane maker Airbus, she said, Boeing must push toward keeping only that work at Auburn and driving out mature technologies to supplier partners.
"The only way we'll survive is if we stay out ahead and pull them along," she said.
Boeing is outsourcing low-complexity machining work from Auburn to Pakistan, Romania, South Africa and Turkey to offset earlier jet sales to those countries.
A Boeing internal document obtained by The Seattle Times estimates that the outsourcing of that work will mean about 100 fewer machine-shop workers. However, Auburn site director Paul Nuyen and Armstrong said there'll be no on net reduction in employment because of the new programs.
"We stabilized those machine shops. We've hit bottom," said Nuyen. "(The new programs) will more than mitigate the reductions."
"We think we are sized approximately correctly," Armstrong said. "We expect a little bit of moderate growth."
Despite that optimistic outlook, the strategic decision to develop and then push out more complex work bothers Mark Blondin, president of Machinists union District 751.
"I don't accept that once they've developed this, you give it away," said Blondin. "This whole country is tired of this outsourcing concept."
Tom Riley, a team leader on the production floor, said the plant had recently outsourced production of 777 end frames to a supplier in California.
"It's disappointing to see good work, where we've ironed out all the problems and got a good sleek manufacturing process, and all of a sudden it's gone to California," said Riley.
He's not convinced by management assertions that work going out will be replaced by new development work and by "emergent" work — work that arises unexpectedly because of a glitch in production or some short-notice customer request.
"If you don't keep some basic work in here to keep us going when we don't have something emergent, then what happens to Auburn?," he said. "Does the place shut down as soon as we're done working this new airplane out?"
But management is set on its course and that work will not dry up for its Auburn employees.
What happens when the three large cargo freighters are in service and the 7E7 is in production?
"There's always another next thing," said Deborah Dustman, spokeswoman for Boeing's fabrication division. "You've got to be ready to do the next new thing."
Dominic Gates: 206-464-2963 or dgates@seattletimes.com
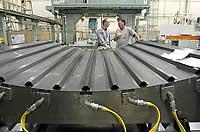