Boeing shares work, but guards its secrets
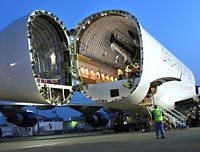
The first wings for the 787 Dreamliner landed in Everett early this morning, ready-made in Japan.
In a sharp break with the past, the 787's wings are made out of composite plastic rather than metal. But, just as revolutionary, Boeing delegated to Mitsubishi of Japan a big slice of the design work.
The 787's unparalleled sales success — jump-started by a 50-jet order from Japan's All Nippon Airways — has burnished the Puget Sound region's reputation as a world center of commercial aviation.
And yet global outsourcing of Boeing work is an inextricable part of the ambitious 787 manufacturing plan, diminishing the region's role.
Did Boeing give away the "crown jewels" to Japan, jeopardizing the company's future by sharing its exclusive know-how with potential competitors?
The wings of an airliner are a crucial feat of engineering magic. They flex upward as they lift enormous loads into the sky. A complex system of movable edges lets the pilot control the plane. And the wings hold thousands of gallons of jet fuel just beneath their skin.
On all previous jet programs, the entire wing design was done by Boeing's engineers in Everett.
Stan Sorscher, a research analyst with the white-collar union at Boeing, the Society of Professional Engineering Employees in Aerospace (SPEEA), criticizes the outsourcing of Everett jobs and fears it will erode the company's expertise.
Company executives say Boeing kept for itself the top-level design work without which the Japanese couldn't even begin. Boeing isn't giving away the store, they insist.
"I understand why it sometimes looks that way to someone who doesn't understand the process," said Mark Jenks, leader of Boeing's 787 wing team. "I'm not at all worried."
Comparison to iPod
When it comes to the globalization of airplane building, industry analyst Richard Aboulafia likens Boeing to Apple — and a $150 million Dreamliner to a $300 iPod.
"Apple invented the iPod, markets it, sells it, supports it, and integrated the whole concept. But they don't care about building it," Aboulafia wrote in a letter to clients. "With the 787, Boeing is moving in Apple's direction."
The globalized 787 business model is meant to save money — not through cheap labor, but through sharing the up-front investment with others, he said.
Boeing's 787 partners carry big pieces of that burden. In return for the contracts to make huge 787 sections, they've invested billions of dollars, tapping whatever subsidies they can.
Japan's government provides loans estimated at up to $2 billion to the three Japanese partners. Italy provides regional infrastructure support to Alenia. In the U.S., South Carolina and Kansas provide financial incentives to Vought and Spirit AeroSystems, respectively.
"It's all about spreading the cost and the risk," Aboulafia said.
Bob Noble, the Boeing vice president responsible for global partners on new programs, said a partner's ability to invest, reducing Boeing's upfront costs, is "a big consideration" when deciding which companies participate.
But another big factor is finding the needed engineering talent and technical capacity.
"We have to be global," Noble said. "It's a whole world full of people's talents and capabilities we're bringing together to make this."
"The family jewels"
Jenks, who leads the wing team, said the crucial, conceptual stage of the 787's wing design was "100 percent Boeing."
To define the shape of the wing and the system of movable flight-control surfaces, Boeing aerodynamicists conducted detailed analysis of performance requirements, historical flight-test information and new wind-tunnel data.
Only after that defining phase of the 787 design did Boeing bring Mitsubishi engineers to Seattle to figure out the broad parameters of the internal structure of the wing.
"We gave them the shape," Jenks said.
"That is the family jewels," Noble said. "That part I could never see Boeing sharing in any way, shape or form. That is what our brilliant engineers are able to figure out."
Boeing engineering legend Joe Sutter, lead designer of the iconic 747 jumbo jet in the late 1960s, agreed that this first design phase is the key.
"That's the stuff that Boeing still pretty much keeps under its own belt," said Sutter, who at 86 still talks at aviation gatherings about jet design.
The grand bargain that underlies Boeing's global manufacturing approach is worth it, Sutter said.
"Boeing still has that know-how," he said. "Maybe the Japanese learned some of it, but for what they bring to the market, Boeing is winning, not losing."
Boeing handed off to Mitsubishi the detail work of designing on computers the ribs, spars, skins and other components of the wing, before actually building the parts.
The global partners use an expensive software system to enable real-time collaboration among engineers in Japan, Italy, Russia and the U.S., all working off a digital copy of the 787 design that's held on central Boeing servers in Bellevue.
Princeton University economist Alan Blinder sees a growing pattern of outsourcing of surprisingly high-level work through such electronic means.
"There's no relationship at all between vulnerability to offshoring and skill level," Blinder said. "What makes it offshorable is whether the service can be delivered over a long distance electronically."
He estimates 30 million to 40 million U.S. jobs could be lost over the next two decades through Boeing-style communication technology. Old-school Boeing engineer Sutter acknowledges the local impact of losing the detailed design work.
"The big loss is you are going to be shrinking your labor force here," he said. "The young start-up engineers, there's less of them required. Yes, jobs are disappearing."
Work-force concerns
Naturally, letting go of work at any level upsets local Boeing workers, whether machinists or engineers.
SPEEA's Sorscher fears the company is hollowing out the aerospace expertise built up in this region over decades.
The 787 wing is the first large airplane wing made from carbon-fiber-reinforced plastic composite. Some of the expertise in working with that material was first developed for the B-2 bomber program in the 1980s, paid for with U.S. government money.
"If 10 or 15 years from now the world's leading authority on this kind of structure is in Japan, then you can't reallocate your resources to do that work," Sorscher said. "You are dependent on them."
And he warned that the "fragmented global supplier network" creates new risks for the plane's development.
When problems arose on previous airplane programs, Sorscher said, Boeing would throw people and money at the problem, relying on its local engineers to devise solutions.
But with 787 work outsourced around the globe, he said, "it's harder to coordinate, harder to realize you have a problem, and harder to reallocate resources."
Jobs for the Japanese
A year ago, at the peak of 787 development work, between 300 and 400 engineers from Mitsubishi Heavy Industries, Kawasaki Heavy Industries and Fuji Heavy Industries worked in Seattle and Everett alongside Boeing colleagues designing Dreamliner parts.
By now, all have returned home, where the so-called Japanese "Heavies" — the three heavy-industrial companies that share 787 work — have built costly new facilities for Dreamliner production.
It may look like a steppingstone for another ambitious Japanese industrial sector that could displace U.S. production. But Aboulafia sees quite the opposite — a Japan desperately subsidizing its aerospace industry to keep high-paying jobs from disappearing.
"It's fiefdom protection, jobs for the boys," said Aboulafia, who has studied the aviation industry in Japan. "Given the disastrous downturn in Japanese military aerospace since 1990, they are protecting what's left."
Aboulafia said that provided "Japanese government largesse" continues — with more loans to fund Boeing's next jet development — Japan could well build future Boeing wings.
So is Mitsubishi now Boeing's official wingmaker?
Not necessarily, said Boeing's Noble. Mitsubishi's new 1.2-million-square-foot Nagoya facility has room to build only the 787 wings.
"They'll need to earn their way onto future models the same way they earned their way onto this one," Noble said.
But whoever the future partners may be, the 787 manufacturing plan is now Boeing's template for subsequent programs.
Noble said he can't imagine Boeing ever again building a jet airframe largely on its own.
At the same time, he said, the Dreamliner plan probably pushes outsourcing just about as far as Boeing will go.
"The 787 defines the place we want to be," Noble said.
Monopoly in Japan?
Since the beginning of the jet era, Japan has spent more money buying Boeing airliners than any other country.
The Boeing orders placed by its airlines cannot be formally pegged to the amount of manufacturing work the company locates there, because World Trade Organization rules forbid such deals.
But the top executives of the nation's aerospace industry, airlines and banks are bound by social ties and serve together on government-appointed industry bodies.
The upshot is that Japanese airlines' jet orders complement the nation's manufacturing strategy.
Boeing gives the Japanese work, and Boeing secures a virtual monopoly in jet sales.
All Nippon Airlines and Japan Air Lines have together ordered 85 Dreamliners. And Nippon Cargo Airlines was a launch customer for the new derivative of Boeing's jumbo jet, ordering eight 747-8s.
That decades-long dominance in Japan is a sore point with Boeing's global rival.
Airbus chief spokesman Rainer Ohler said the European planemaker is "trying everything" to enter that market, with the new A380 superjumbo its best hope.
"If we don't make it with the A380 in Japan, we will never make it there," Ohler said.
Airbus plans to outsource half the work on the upcoming A350 jet, which will compete with the 787. But it has little prospect of breaking into Japan that way because all the Japanese "heavies" are working flat out on Boeing programs.
"It is not easy now to find open doors," Ohler said. "We don't expect much in Japan with the heavies."
Dominic Gates: 206-464-2963 or dgates@seattletimes.com
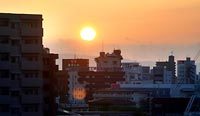
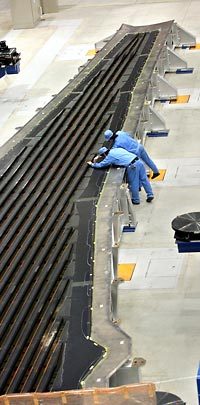
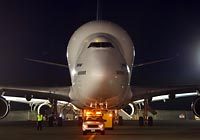
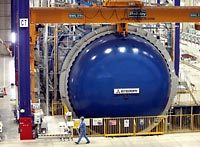
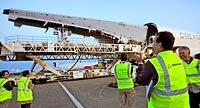
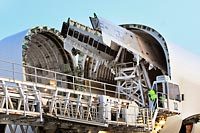
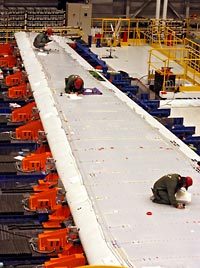
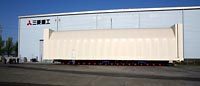


Three Japanese industrial giants build and co-design 35 percent of the 787. They deliver most of the 787's center section and are now manufacturing the massive composite plastic pieces in Nagoya, two hours southwest of Tokyo by bullet train.
The Japanese government provides loans to finance the development project estimated at up to $2 billion.
Mitsubishi Heavy Industries builds the main piece of the 114-foot-long 787 wing and attaches the fixed trailing edge built by Kawasaki and the fixed leading edge built by Spirit AeroSystems in Tulsa, Okla. The two big wing sections delivered to Everett together weigh about 25 tons.
Kawasaki Heavy Industries builds the fixed trailing edge of the 787 wing, which it delivers to Mitsubishi. Kawasaki also builds the barrel-shaped, single-piece fuselage section just forward of the wings. The fuselage section, weighing about 5 tons, goes to Global Aeronautica in Charleston, S.C., for assembly.
Fuji Heavy Industries (better known as the maker of Subaru autos) builds the 787's "center wing box," the load-bearing structure in the lower central fuselage that holds the wings. The Fuji part, delivered to Charleston, S.C., weighs almost 10 tons.
Source: Boeing