Flow International's tools to cut 7E7 wings in Japan
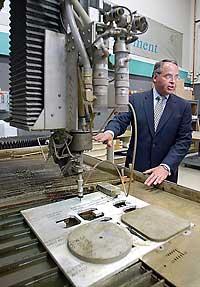
Flow International's waterjet industrial tools are already used to cut the materials for disposable diapers, to lathe long skinny carrots into supermarket "baby carrots," to carve out Chicken McNuggets and — with abrasive sand added to the water stream — to slice through thick metal and hard plastic materials.
To cut aircraft parts, a thin stream of water moving at three times the speed of sound is shot from a tiny jeweled orifice in the tool head of Flow's machine. The gallon-per-minute water flow sucks in a separate stream of pink garnet sand that slices into the surface to be cut.
The large waterjet machining system for the 7E7 wings, 105 feet long and 20 feet wide, will be built and tested in Jeffersonville, Ind., at one of Flow's six worldwide plants. The high-tech, ultra-high pressure pumps that power it will be made at the Kent headquarters.
"We expect to deliver it to Japan and to be making wings next fall," said Flow's CEO Stephen Light.
Until his Japanese customer is ready to announce, Light won't name the buyer. But a Flow preliminary drawing shows the 7E7 wing skins in the machine tool; Mitsubishi Heavy Industries is the company building these parts of the 7E7.
And there may be more 7E7 work to come.
Light said Flow, which has three offices in Japan, is also talking to the other major Japanese 7E7 partners, Kawasaki Heavy Industries and Fuji Heavy Industries, as well as ShinMaywa, a likely second-tier supplier.
"Each is acquiring waterjet machines, none quite as large as the wing machine," Light said, "We are aggressively pursuing all the 7E7 content we can."
In Wichita, Kan., Raytheon uses a Flow abrasive waterjet tool to cut the single-piece fuselage of its all-composite Premier business jet.
"The technology on the Raytheon Premier jet is essentially the same that Boeing is going to employ on the 7E7," Light said.
Out of Boeing
Flow was founded by two former Boeing scientists in the 1970s. One of them, John Olsen, left Flow in the early 1990s to found another waterjet company, OMAX, also based in Kent.
OMAX, a smaller company with about 70 employees, competes with Flow in the market for smaller standardized industrial waterjets, but doesn't make giant customized machines such as the 7E7 tool.
One of Flow's selling points is that it supplies a complete solution to its customer: the high-pressure pump, the cutting head, the machine fixture, the robotics, the software.
In doing so, it integrates technology from its own suppliers, including some local ones.
The 7E7 wing machine for Japan will likely incorporate computer-controlled shafts for holding the parts in position, developed and built by CNA Manufacturing Systems, a small Woodinville company.
Flow's first large industrial application was in the cutting of diapers and paper products. In 1980, Flow senior vice president of technology Mohamed Hashish, still with the company, invented the abrasive waterjet process — adding sand to the water stream — which revolutionized the field and enabled many more applications.
Carl Olsen, an engineer at OMAX and the son of John Olsen, said that since then software developments have enabled precise control of the robotics and machine settings, so the precision of the cutting has increased.
Big and small uses
As a result, waterjets are becoming ubiquitous in machine shops, big and small. About 40 percent of Flow's business comes from small machine shops with fewer than 10 employees.
"It's like a lathe," said Olsen, "It's a general-purpose machine tool."
There certainly are large industrial applications, too.
Waterjets are extensively used in the automotive industry — the dashboard on any American-built car has been cut with a waterjet.
Boeing, a longtime customer, uses large waterjets to cut the composite tail section of the 777 in Frederickson, near Tacoma.
And Flow provided the Airbus unit in Spain with waterjets to cut the tail sections for the A380 superjumbo.
Though there are now dozens of waterjet companies, Flow has installed more than 7,000 of its tools and claims a 62 percent market share worldwide.
"They are definitely a dominant player in waterjets," said Alan Davis, a financial analyst with McAdams Wright Ragen. "But their competition is not just waterjets. Their challenge is convincing people to use waterjet technology over traditional cutting methods."
Despite its market share and impressive technology, the company has struggled in the past few years.
The downturn in manufacturing hit the machine-tool business hard just when the company took on massive debt to make an acquisition and diversify. Flow had to lay off about 20 percent of its employees.
Light, brought in 18 months ago to turn the company around, is more than halfway through a two-year restructuring plan and has extended the current debt agreements by a year.
Last quarter, Flow lost $3 million on sales of $54 million, compared with a loss of $16 million on sales of $32 million a year earlier.
"We're finishing the beginning of the recovery," he said. "The company is now profitable on an operating basis."
Abrasive waterjets have emerged as a literally cutting-edge technology in aerospace manufacturing in part because of the increasing use of advanced composite materials in new airplanes. Most of the 7E7 airframe will be made from plasticized laminated carbon.
Traditional milling machines with metal cutting heads can damage composites: the shear forces across the surface can delaminate the material and the heat generated can damage it.
Since waterjet technology acts by the grinding effect of minute particles, there are no shear forces. And since the cutting tool is kept one-tenth of an inch from the material and the water stream acts as a coolant, the work generates little heat.
The lack of contact between tool head and the part being cut has other important benefits: The tool head doesn't grow dull, and the entire fixture can be lighter because it doesn't have to withstand massive forces as it holds the part in position.
Yet the process of cutting through 16 inches of steel or carbon composites with sand and water isn't effortless nor inexpensive. The tube where the sand and water mixes must be replaced every 120 hours or so of operation due to wear.
With the rise of aerospace composites, Light sees a sharp increase in airplane manufacturing orders ahead. Yet even with Flow's tools in use on both the Airbus A380 and the Boeing 7E7 — the two great commercial airplane programs of the next 20 years — he estimates that aerospace will be about only 10 percent of the company's business.
Despite the application of its tools to airplanes, Flow is glad to be still in diapers — and lots of other products.
Dominic Gates: 206-464-2963 or dgates@seattletimes.com
![]() |