Local firm finds $200 million niche helping Boeing rival
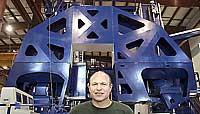
Inside, giant 150-ton, automated machines straddle sheets of aluminum, drilling and riveting them to create skin panels.
Cranes then move the metal skins, ribs, and spars into position on heavy assembly jigs — four-story-tall fixtures anchored deep in the ground — where men and robotic machines traverse the structure and fasten together the largest commercial aircraft wings ever made.
A month ago, barely a mile from Boeing's Everett plant, Peter Zieve had sketched a diagram of this factory a continent and an ocean away.
"We own this," said Zieve, 50, president of Mukilteo-based Electroimpact, sweeping his hand across his whiteboard drawing showing the layout of rows of automated riveters and assembly jigs. "This is our territory."
He wasn't exaggerating. Most of this heavy equipment here in Broughton, the machines and the fixturing that fills most of the plant, was designed and built by Electroimpact.
For its work on the A380 contract alone, Electroimpact will reap revenues of roughly $200 million.
A small company with an elite engineering culture, Electroimpact was born out of Zieve's doctoral work at the University of Washington when, ironically, he developed a technology to solve a problem posed by Boeing.
But Airbus, which has supplanted Boeing as the world's No. 1 commercial-aircraft manufacturer, is by far his best customer.
At the Farnborough Air Show, which ended a week ago in London, the most intense focus was not on Boeing's 7E7 but on the 555-seat A380.
"(Electroimpact) has played a key part in the A380 program," said Iain Gray, managing director of Airbus United Kingdom. "They've allowed us to bring increased levels of automation into our business."
Electroimpact makes automated, computer-controlled machines for drilling, riveting, and bolting aircraft parts, along with integrated jigs — called the tooling — that hold the aircraft parts precisely in place so that they can be fastened together in accurate alignment.
For the A380, Electroimpact introduced new robotic drilling machines that partially automate the traditionally manual process of assembling the wings.
The first set of A380 wings came off these Electroimpact jigs in April and shipped out of here for final assembly in Toulouse, France. By next year's Paris Air Show, the first A380 will fly in.
"I'm incredibly proud of what we did on the A380," said John Hartmann, 46, Electroimpact's vice president, who runs the company with Zieve. "It meant cold sweats for months, but it's very fulfilling."
An engineering culture
Besides its work for Airbus, Electroimpact ships tooling to Israel for manufacture of the Gulfstream 150 business jet in Tel Aviv.
And though relations with Boeing were rocky in the early years, Electroimpact has sold smaller, less sophisticated automated riveters to its neighbor and has a couple of high-tech Boeing projects.
Indeed, the company would like to expand its Boeing business by doing for the 7E7 program in Japan what it does for the A380 program in Britain.
An engineering team is working on various proposals with the 7E7's Japanese suppliers, who will build that airplane's composite wings, developing concepts for the tooling that will be needed.
Electroimpact employs 210 people in Mukilteo, 10 in Tel Aviv and 50 on the spot to service Airbus here in Britain. About 60 percent of the employees are engineers, and it is they who rule the roost.
Having assembled the best and the brightest — every job applicant must pass a stiff written test — Zieve gives employees a high degree of freedom. Each engineer has "a little red book" for noting down any purchasing requirements, which are processed weekly.
When Zieve started the company, he said, "The engineers asked me, 'Don't we have to get approvals?' I told them: 'No. The engineers are the approvers.' "
And working on the most prestigious commercial-aerospace project in the world — the A380 — clearly raises the energy level.
That's something most Boeing engineers, absent a new airplane program, have been missing for years and that they dearly hope will be recaptured with the 7E7.
Ted Karagias, 33, a mechanical engineer who has been with Zieve six years, previously worked on the 777 program at Boeing, an experience he described as "mind-numbing."
But when he was brought in to work on the early conceptual-development phases of the A380 project in 2000, he was transformed into a true believer embarked on changing the world.
"I remember lying on my back on the conference table, thinking of ways to build things," Karagias said.
Now focused on completing the next A380 jig and developing something similar for the A400M military transporter, he still feels like he works in a "a romper room for engineers," a paradise where everything is hands on.
As Karagias spoke in Mukilteo, behind him Tim Van Horn — a 45-year-old engineer whom Zieve described as a leading expert in Unigraphics computer design software — stood atop the frame of a fixture he'd designed for the Israeli-built Gulfstream jet project. With two others, Van Horn eased a metal beam into position with a crane.
"The engineer at Electroimpact wears not just a design hat, but every hat: design, execution, production, assembly, shipping, installation," Karagias said.
In Broughton, Pete Goldsmith, 27, a lanky Canadian engineer who stands 7 feet tall in his heavy workboots, recalled making the mistake of wearing a suit on his first day at Electroimpact in 2002. He found himself chopping steel with a bandsaw.
"What you design, you have to physically build," said Goldsmith, who leads the A380 assembly-jig project in Broughton. "You rapidly find out all the mistakes you made at the computer."
The engineers relish that do-it-yourself challenge.
"You have to do everything here," Karagias said. "It's an awesome place to work."
Automated riveters, jigs
Electroimpact first made its mark with Airbus by providing large automated machines that perform the first stage of wing construction.
The machines create wing "skins," the top and bottom surfaces of a wing, by drilling holes in metal panels — 80,000 holes per wing — and riveting them together with long stiffening rods called stringers that run the length of the wing.
The work is fully automated: the panels and stringers are clamped in place on an integrated fixture and the riveter moves along rails and does all the fastening.
After supplying the riveters for the big A340-600 project in the late 1990s, Electroimpact had plenty of cash but not enough work. Boeing, licking its wounds from the 1997 production crisis, had stopped spending money and wasn't launching a new jet, so there was no opportunity there.
The Mukilteo company shrank from 160 employees to half that, hanging onto its best people, while its executives sought the next big thing.
"I spent a lot of time in Broughton," Hartmann said, "I said, 'What do you want us to work on? I have this talent; let's put it to use.' "
The A380 program — not yet officially launched then — was in gestation, and Airbus asked Electroimpact to go beyond tooling for skin panels and to reinvent also the next and crucial phase of wing making.
The basic wing is formed by fastening together a ladder-shaped structure of front and rear spars with transverse ribs, then adding the upper and lower skins. Previously, this process has involved intense manual work. All the pieces would be held in a jig while mechanics drilled another 20,000 holes per wing and riveted them together by hand.
Electroimpact engineers set about designing a jig that would hold the immense wing — 148 feet long, 36 feet wide, almost 10 feet thick at the root-end where it ultimately attaches to the fuselage, and weighing around 33 tons — and allow for the first time at least partial automation.
In the summer of 2000, an Airbus manager came to view a full-scale model of the first jig concept for the inboard section of the A380 wing, represented by a plywood dummy. The drilling machine was monstrous, six-stories-tall. "He walked in the building and said 'Never'," Hartmann recalled, "We were completely deflated."
But his engineers went back to the drawing board and came up with the design that's in place in Broughton today: Instead of a monster machine, they went for what Hartmann described as "little local machines crawling over the structure."
Moving from one floor of the jig to the next, two computer-controlled, robotic machines do some of the heaviest drilling, such as that on the thick landing gear ribs. Other drilling and all the riveting and bolting is still done manually.
As part of the deal with Airbus, Electroimpact subcontracted about 60 percent of the work of building the jigs to six local firms in Britain. But all the high-tech robotics was done in Mukilteo.
Hartmann was impressed at the faith Airbus showed in his team, tasked with delivering equipment without which the airplane simply couldn't be built.
"I felt like I worked for Airbus. I wasn't treated as a supplier. I felt very much at home," Hartmann said. "In turn, we killed ourselves for the A380. We worked 20 to 24 hours a day, seven days a week for six months to get those wings in production on time."
Asked how much money the A380 means to Electroimpact, Hartmann — who described himself as "the nearest thing we have to a CFO" — turned to a whiteboard and wrote a short column of numbers, which he totted up for a running total of $181 million, before turning around, still adding in his head.
"It'll be over $200 million when we're done," he said.
As the A380 ramps up toward full production, Electroimpact has to pump out more tooling.
The company already has delivered four gigantic automated riveters for the A380 wing panels, with two more nearing completion in the Mukilteo factory. Airbus could require up to 10, depending on orders.
The company has also installed three of the A380 wing assembly jigs in Broughton, and Airbus wants one more.
The same design team is now working on a wing-assembly jig for the next big European aircraft project: the A400M turboprop-military transport, set for first flight in 2008, to be built by Airbus Military, an Airbus-led seven-nation consortium.
Pete Goldsmith expects to leave Wales and head to Filton, England, for that project sometime next year.
And there are other customers.
At the Farnborough Air Show last week, Tom Risley, CEO of Vought, described his plans to close down a plant in Nashville, Tenn., and consolidate operations in Dallas, Texas.
The Nashville plant, which makes skin panels for Airbus A330 and A340 airliners, uses Electroimpact automated riveters.
Risley plans to buy completely new "state-of-the-art" tooling equipment for the consolidated operation in Dallas. And he's looking again to Electroimpact.
"They're top of our list," Risley said. "We're going to the latest machines that they have."
Yet, the biggest prize Electroimpact is shooting for is a place on Boeing's 7E7.
That airplane's wings, to be built by suppliers in Japan, will be made from composite materials, similar to the A400M.
Zieve couldn't be prouder of what he's achieved for Airbus in the United Kingdom.
"I'd love to do the same thing in Japan," Zieve said.
Dominic Gates: 206-464-2963 or dgates@seattletimes.com
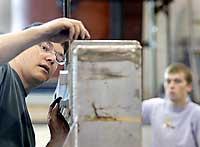
![]() |